Nesta série de blogs, discutiremos a mais recente tecnologia de monitorização baseada em condições para equipamento rotativo.
Em primeiro lugar, gostaria de vos falar sobre a necessidade urgente de os negócios industriais encontrarem uma solução melhor do que as soluções tradicionais de monitorização de motores.
A minha próxima publicação examinará detalhadamente como a análise de assinatura de corrente do motor (MCSA) está a responder a esta necessidade.
Reduzir o elevado custo dos tempos de inatividade: um desafio de todo o setor
Foi relatado que, em média, os custos de inatividade da indústria rondam os 25 000 € a 40 000 € (29 000 a 47 000 dólares americanos) por hora. No entanto, para alguns setores como o fabrico de automóveis, isto pode chegar a 42 000 € (50 000 dólares americanos) por minuto! Estes custos referem-se a perdas de receita, custos de recuperação e, em alguns casos, a sanções e multas com base em acordos ou regulamentos de nível de serviço.
As falhas de motores elétricos são uma causa comum de tempo de inatividade não planeado. As máquinas rotativas acionadas por motores de indução CA de baixa ou média tensão representam a maioria das aplicações industriais, desde petróleo e gás, passando pela mineração, marinha, aeroportos até centros logísticos.
Além dos motores, o equipamento rotativo pode incluir bombas, compressores, transportadores, sopradores ou ventiladores, rolos ou moinhos, etc.
Com 20 a 25 por cento dos motores elétricos a serem cruciais para as operações e uma taxa de falha anual típica de até 7 por cento, os motores têm um grande impacto no tempo de inatividade e nas perdas. Além disso, quaisquer reparações necessárias são geralmente feitas durante o horário de funcionamento, causando mais tempo de inatividade.
O Gabinete de Tecnologias Industriais do Departamento de Energia dos Estados Unidos estima que os motores representam 60 por cento do consumo de energia elétrica nas indústrias de manufatura e até 90 por cento nas indústrias eletrointensivas.
Por conseguinte, encontrar formas de melhorar a eficiência pode fazer uma grande diferença nos resultados financeiros de uma empresa.
Por estes motivos, as organizações precisam de adotar uma estratégia de manutenção mais preditiva, para ajudar a evitar reparações e tempo de inatividade não programados, e para melhorar a eficiência, reduzir custos e extrair vidas úteis mais longas do equipamento rotativo.
Isto requer o suporte da monitorização e da análise preditiva baseadas em condições para equipamento rotativo.
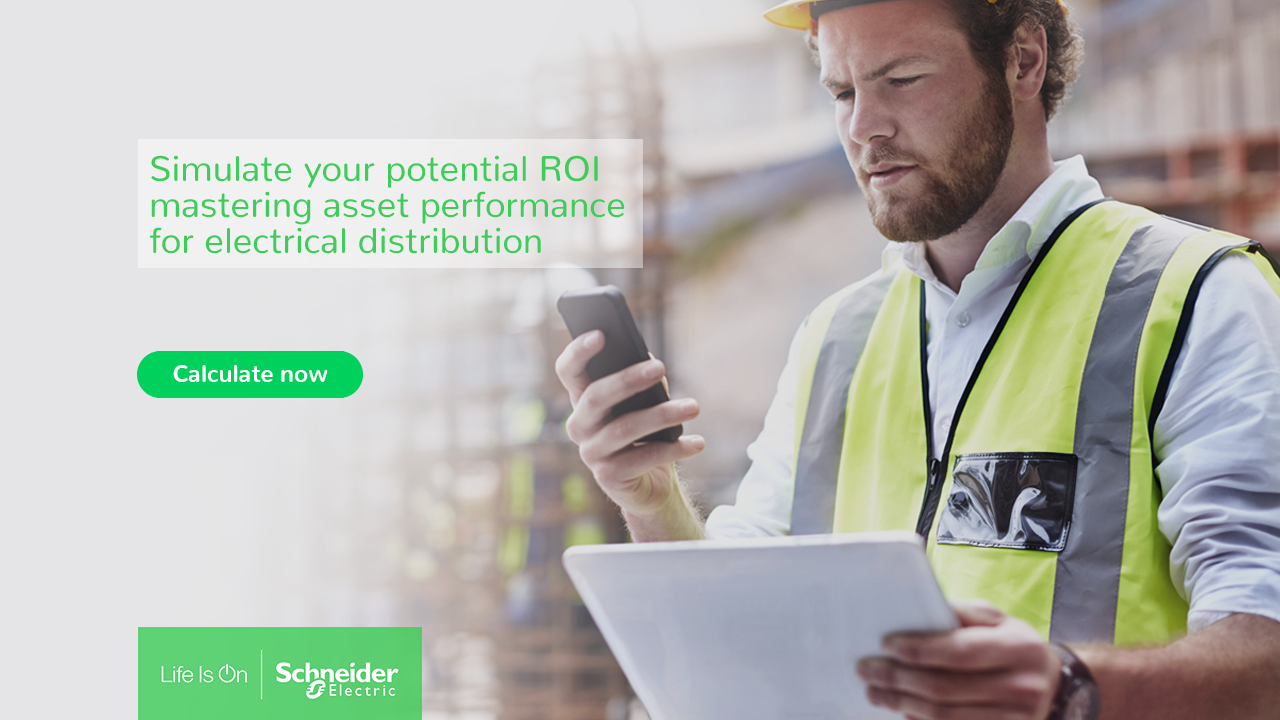
Manutenção preditiva vs. manutenção tradicional do motor
São utilizadas várias estratégias de manutenção no ambiente industrial. Se uma equipa de manutenção utiliza o método de ‘funcionamento até à falha’, essencialmente, é feita uma manutenção mínima ou nenhuma manutenção num motor até que ele falhe completamente.
Obviamente, a organização deve aceitar então o tempo de inatividade não planeado como parte das suas operações regulares. Se for utilizada uma estratégia preventiva, a manutenção é feita em intervalos definidos – por calendário ou horas de funcionamento – com o objetivo de atingir um nível de disponibilidade baseado em estatísticas de tempo médio entre falhas.
Infelizmente, isto significa que a manutenção é, geralmente, realizada tarde demais – após uma falha dispendiosa – ou cedo demais, podendo incorrer em gastos operacionais desnecessários. E, em última análise, nenhuma destas estratégias considera a condição real do motor.
Uma abordagem muito melhor é a manutenção preditiva, com o trabalho realizado apenas quando o motor precisa dele, ou seja, quando o desempenho se degrada ou se prevê uma falha. No entanto, esta abordagem requer que a condição do motor seja monitorizada continuamente.
Idealmente, a tecnologia precisa de detetar riscos numa fase inicial. Apenas alguns exemplos de condições de risco incluem: degradação dos rolamentos, excentricidades do rotor ou do acoplamento, desequilíbrio mecânico, folga do enrolamento do estator, cavitação da bomba, perturbações harmónicas ou desalinhamento dos eixos.
É importante detetar estes tipos de riscos com antecedência para reduzir danos potenciais, minimizar o desperdício de energia e, o mais importante, minimizar o tempo de inatividade não planeado.
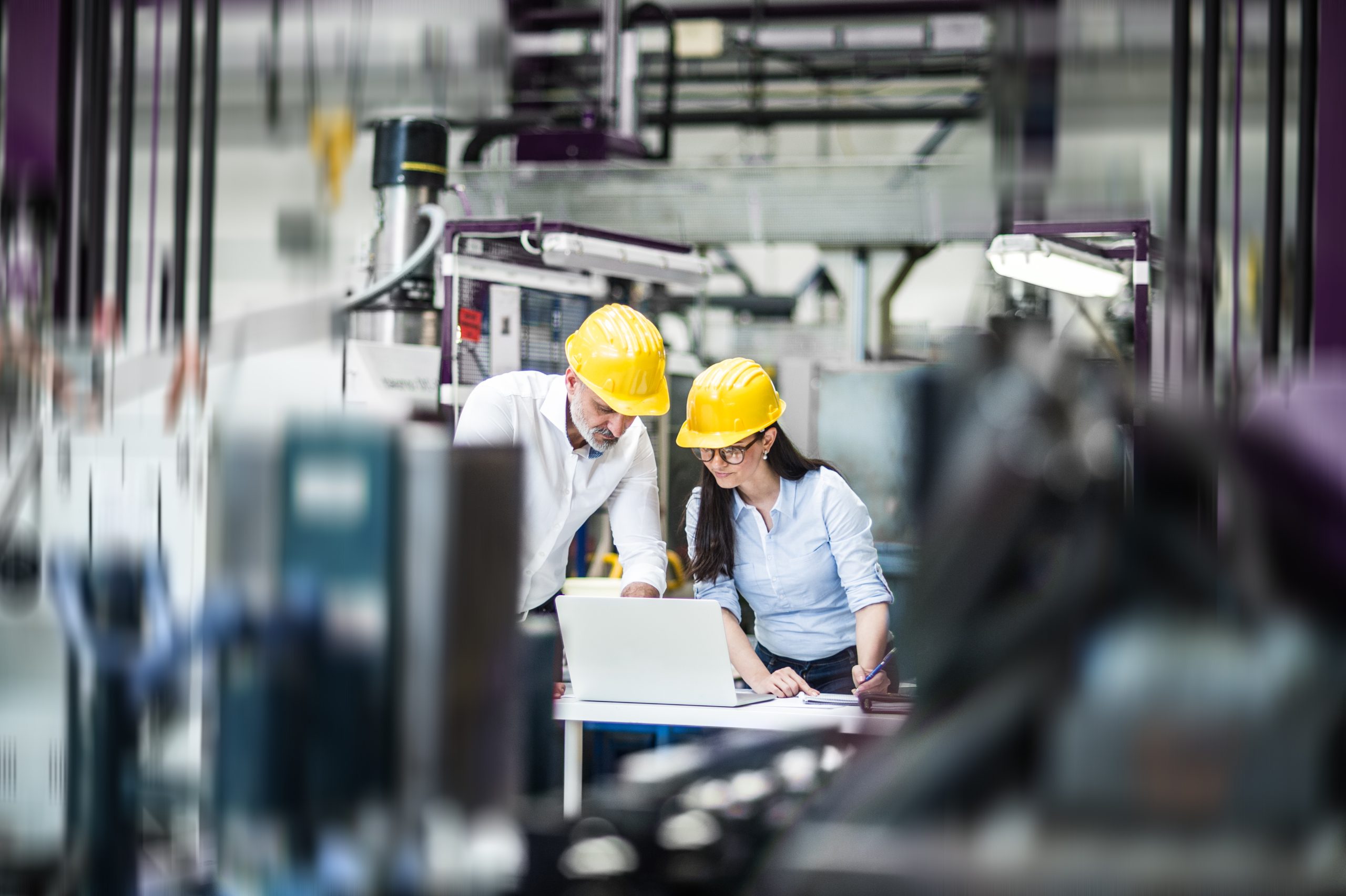
É importante detetar estes tipos de riscos com antecedência para reduzir danos potenciais
Problemas com a tradicional tecnologia de monitorização de motores
Vários métodos têm sido utilizados para monitorizar as condições do motor, alguns deles já com muitas décadas. Cada um tem os seus pontos fortes, mas a maioria tem pontos fracos significativos.
Por exemplo:
- Os sensores de vibração podem ser acionados por ruído ou vibrações do ambiente circundante
- A análise do óleo e a análise de vibrações não conseguem detetar problemas elétricos
- Os sensores acústicos são sensíveis ao ruído de fundo e à interferência de outros objetos
- As câmaras térmicas requerem uma linha de visão direta para os objetos de interesse e são sensíveis à temperatura ambiente e às propriedades térmicas e óticas dos objetos a monitorizar
Para todas as tecnologias mencionadas acima, os sensores devem ser colocados sobre ou perto do ativo a ser monitorizado, o que significa que não são utilizáveis para motores em locais inacessíveis, tais como os utilizados para drenagem subterrânea, submersos no casco de um navio, ou encapsulados em máquinas maiores.
Também não são ideais para ativos localizados remotamente ou amplamente espaçados, tais como turbinas eólicas ao largo da costa, uma vez que a instalação de sensores será difícil, demorada e dispendiosa.
Além disso, estes sensores precisam de ser alimentados por uma fonte de energia com fios ou por uma bateria que necessita de substituição periódica.
Por fim, estes tipos de sensores podem ficar danificados se forem utilizados em condições adversas, tais como um transportador que movimenta placas de aço quentes, ou zonas ATEX com atmosferas explosivas.
Nos últimos anos, surgiu uma nova tecnologia denominada análise de assinatura de corrente do motor (MCSA), que apresenta muitas vantagens em relação às técnicas mencionadas acima.
A MCSA é uma tecnologia inovadora, baseada em IA que monitoriza os sinais elétricos que alimentam os motores CA e compara as condições com uma biblioteca de impressões digitais de dados.
As suas vantagens incluem: instalação mais simples numa gama mais vasta de aplicações, redução das falhas de equipamentos, vida útil prolongada, redução do TCO e um período de retorno mais curto. Na minha próxima publicação, veremos melhor esta inovação empolgante.